Building Efficiency with Our Annual Model Competition
Each year, our project teams come together for a little friendly competition. Project managers and project engineers build detailed foam board models of their projects for field planning and as references for superintendents and foremen once in the field. This year’s model competition featured the following projects:
Kaiser San Jose — A Kaiser Permanente Center of Excellence Medical Center. We are partnering with Rudolph and Sletten on this project, which is projected to be completed in mid-2027.
Bakar Research and Academic Building — A research and academic building on the University of California, San Francisco’s Parnassus Heights campus. Our team is working with Hensel Phelps to bring this design-assist project to life by 2026.
Burbank Airport — The airport replacement terminal project will add 14 gates and more than 6,600 parking spaces at Burbank Airport to meet Federal Aviation Administration standards. Our team is partnering with Holder Pankow TEC JV on the terminal, set to be completed by the end of 2025.
The model competition is judged by our general superintendent, Travis Smith, and our team of superintendents: Darrell Rogers, Joe Marinelli, and Jake Stipic. Their judgment criteria include everything from unit weights to access roads, laydown areas, safety analysis and considerations, accuracy, and creativity. This exercise puts the project management team in the mindset of the field teams to collaborate and produce the safest, most efficient field installation plan.
Congratulations to this year’s winners, Andrea Ramirez, project manager, and Maitreyee Amale, intern, for their excellent work and attention to detail on the Kaiser San Jose model. Their model featured removable color-coded overlays to indicate curtain wall types and sequencing, material samples, detailed curtain wall scope and specifications, and necessary information about the surrounding area for site logistics planning.
The Role of Glazing Contractors in Tackling Embodied Carbon
Humphrey Yap, Chief Design Engineer
Embodied Carbon
Embodied carbon is the total greenhouse gas emissions associated with the lifecycle of building materials, including production, transportation, installation, and disposal. According to the U.S. Green Building Council, “building envelopes are among the systems that can have the largest embodied carbon impact on a building.” To understand this impact, it is important to know the concepts of Life Cycle Assessment (LCA) and Environmental Product Declaration (EPD) when designing the facade system. LCA measures a product’s environmental impact throughout its life, considering all aspects like energy and raw materials, emissions, and waste. An EPD is a report documenting the environmental impact of a product throughout its life cycle, considering resource use, greenhouse gases, waste generation, and other emissions.
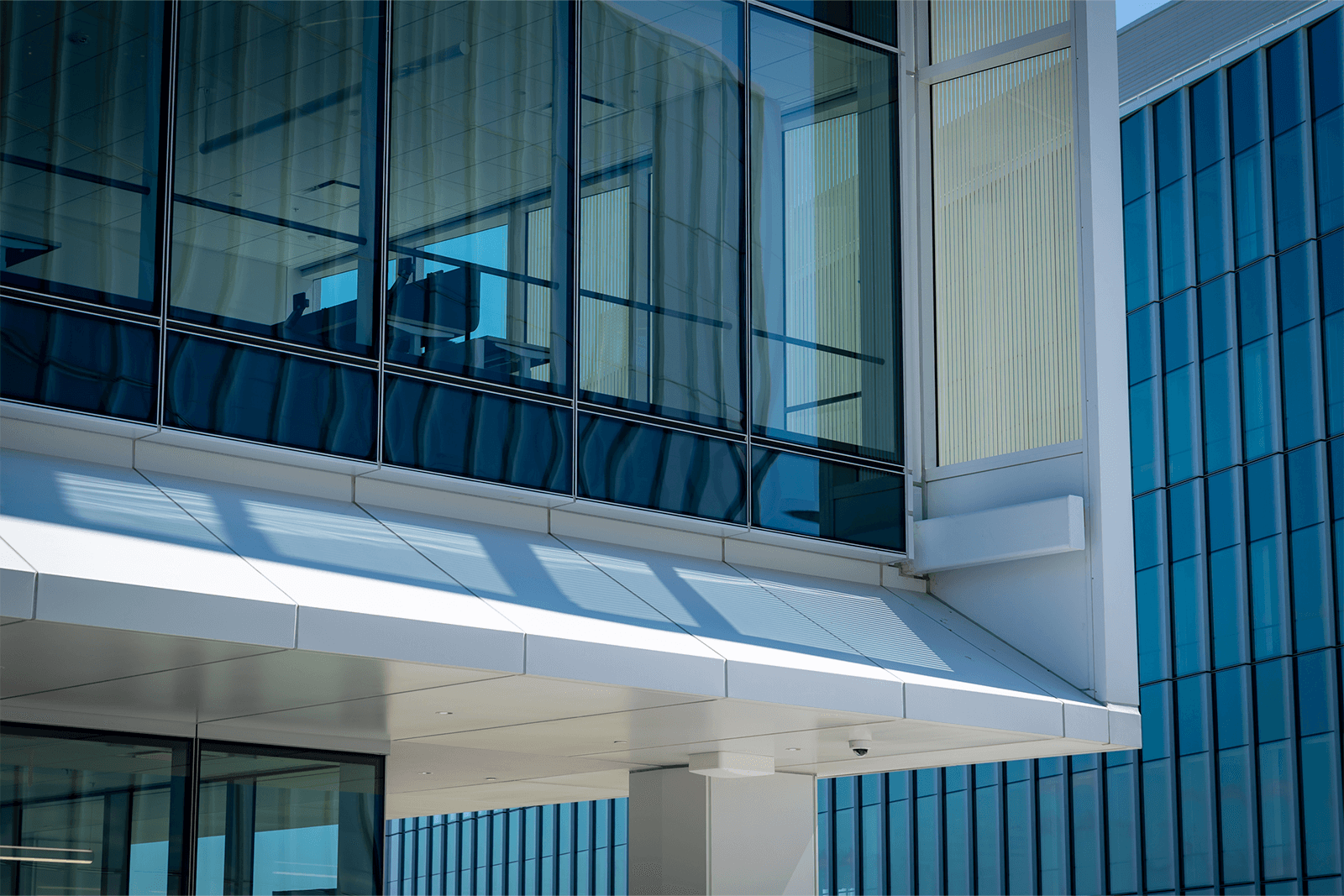
Early Collaboration
As a glazing contractors, we can contribute to reducing the embodied carbon impact of a building.
In collaboration with architects and project design teams, we can offer options for glass products with low embodied carbon, such as recycled or sustainably produced glass.
Design Collaboration
We work with designers to create efficient glazing systems that minimize material use while maximizing performance, like thinner, high-performance glass. Local sourcing of materials reduces transportation emissions and can benefit workforce equity or local business enterprise initiatives on the project. Additional sustainable practices include using all-electric equipment, re-usable bunking, and optimized logistics planning.
Genesis Marina: a TRUE Gold Building
Our recently completed project, Genesis Marina in Brisbane, California, in partnership with SOM and Webcor, is set to become the first commercial building in the world to achieve TRUE Gold (Zero Waste) for Construction certification. While we played a small role in the project, we contributed by using strategies such as delivering all curtain wall units with re-usable bunking and fabricating and installing the curtain wall with electric equipment sourced from our facility in Livermore, California, 50 miles from the job site.
Sustainable Building Practices
Initiatives like CALGreen, the nation’s first state-mandated green building code, and LEED (Leadership in Energy and Environmental Design) lead the charge in the industry and emphasize reductions in embodied carbon. As the industry evolves, our vendor partners are testing and producing higher-performance coatings and energy-efficient framing components to continue to reduce embodied carbon.
Currently, our most effective approach to reducing embodied carbon is through collaboration focused on finding and implementing low-carbon materials and building operations. Engaging with the project team early to establish goals and integrate sustainable materials during the design phase is key to achieving these goals.
For more information on the building envelope’s impact on embodied carbon or to discuss an upcoming project, contact info@aga-ca.com.