Asking the right questions during the bid. Collaborating with your full team to ensure the vision is maintained. Adapting to what we find out on the job site. All while respecting the budget considerations of the overall project. These are our goals on every project.
A proper design-assist requires a commitment from everyone on the project:
estimators, design-engineers, project executives, field superintendents. Our team has to be the DaVinci’s of construction: Part artists, part mathematicians. Engineers with a design aesthetic. It’s not an easy job, but that’s why we love it.
Goals of a Typical Design-Assist
Cost Savings
Ability to identify and evaluate cost savings.
Scope Oversight
Ongoing management of the bid scope as required, utilizing a “trending worksheet”
Change Evaluation
Evaluation of design changes with immediate feedback to cost.
Detail Management
System profiles with a controlled approach to the management of details.
Timely Response
Early resolution of constructability issues.
Efficient Logistics
Early resolution to sequencing and logistic issues.
Upon Initiation
Following receipt of a Notice of Award, a project kick−off meeting is held to confirm the Project Schedule requirements and establish a process for which critical design elements are identified and the process of how they will be resolved in order to meet their respective procurement deadlines.
Design-Assist Meetings
AGA’s project team will attend Design−Assist meetings to verify and complete the exterior facade design and coordinate with other related critical components while conforming with specified performance requirements and adhering to the Project Schedule. This work will be performed with the goal of maintaining the schedule with respect to critical material release dates for the exterior skin. Additionally, the Design-Assist phase meetings shall serve as a forum to identify and address constructability issues with other critical trades and provide a timely resolution.
AGA will proactively ensure the success of the building skin by helping create meeting agendas in advance of those meetings, and highlighting areas of specific need, focus and action by other trades associated with the building skin. We aim to be your hero behind the scenes, ensuring the right questions are asked and the right follow-ups are taken.
The Design-Assist Phase shall be completed upon the successful development of the exterior enclosure system and any other coordination as appropriate.
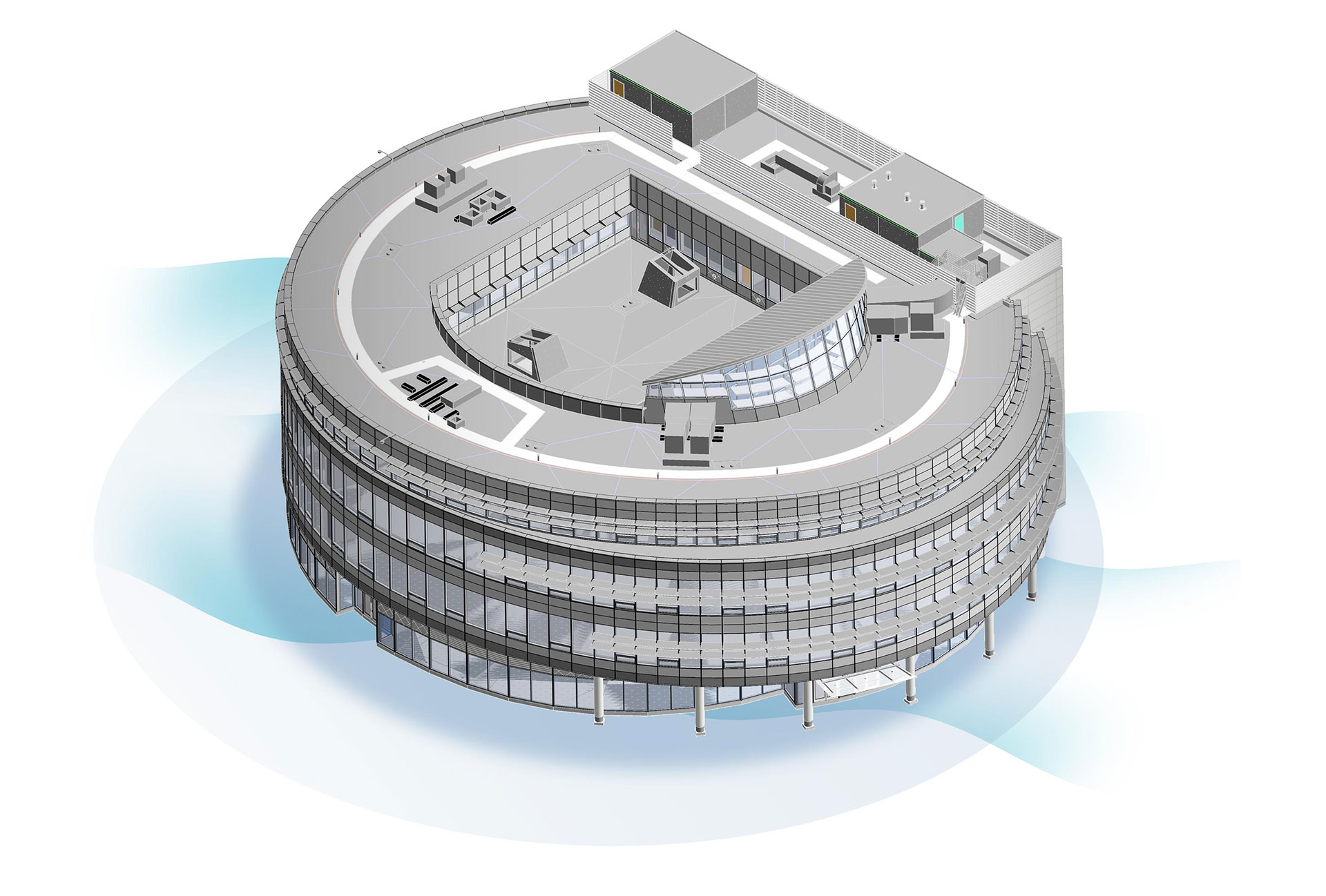
Schedule
One of the first critical priorities is to confirm the scope of work concerning visual and performance mock−ups, since this will establish the priorities for design approval, submittals, and material procurement.
A performance mock−up scope should be decided on early in the design-assist process as the submission drawings for this mock−up will establish the primary curtain wall system design and also dictate material procurement. The performance mock−up test is typically performed by an independent testing consultant at a certified laboratory in California.
Drawings
AGA will typically submit profile drawings for approval by the construction team. This early activity allows us to confirm the aesthetics with the design team while communicating performance with the consultant. The successful completion of this phase will allow die approval and release of the aluminum framing members. Once profile drawings are completed, shop drawings will begin.
Additionally, anchor layout drawings are typically created in Revit to allow for coordination with existing structure and facilitate clash detection with other trades.
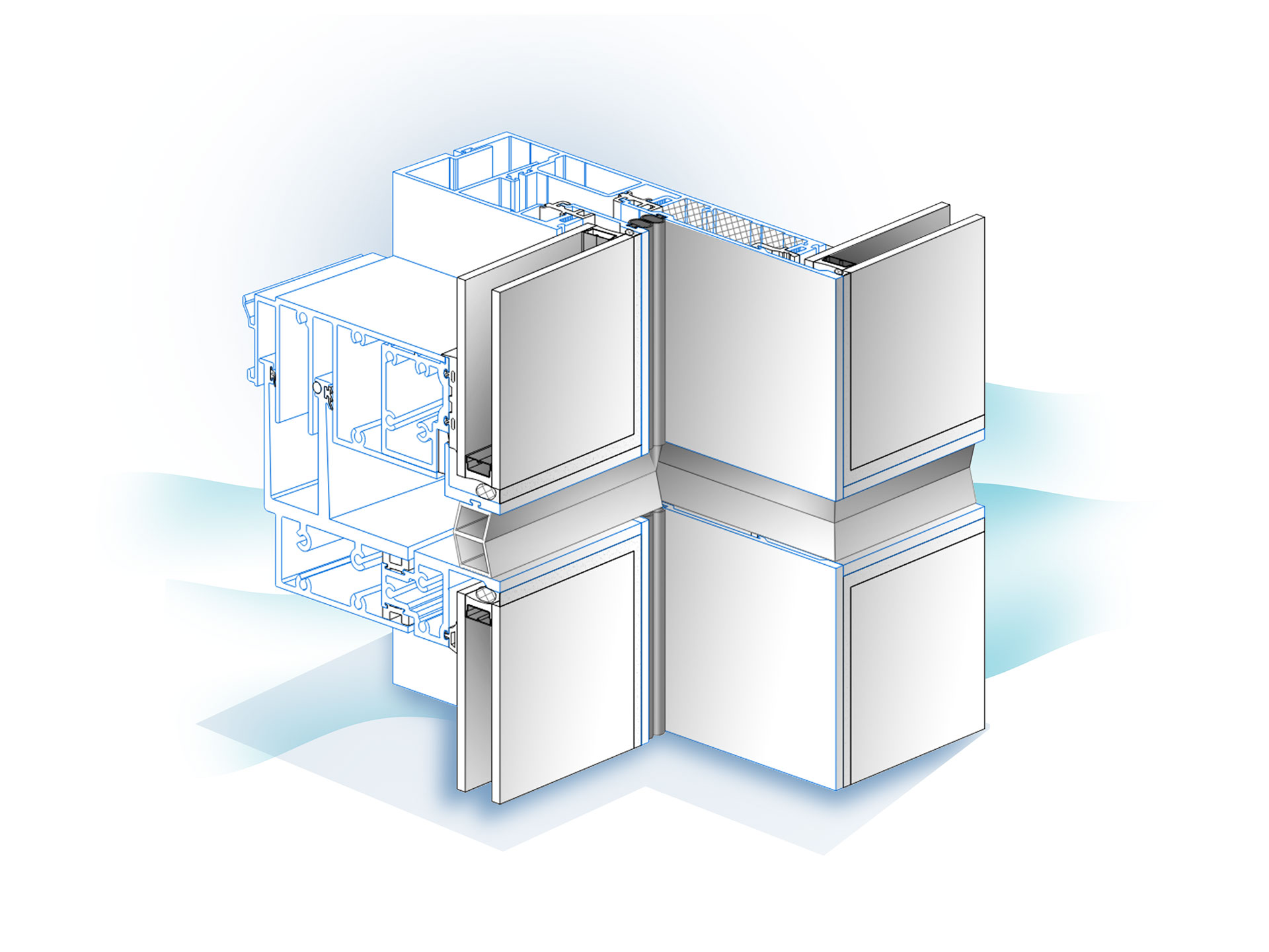
Manufacturing
Material is fabricated at one of our West Coast-based manufacturing facilities. AGA utilizes CNC machine centers in order to maintain the highest level of quality in our fabricated material. Finished goods, assembled in glazed units, are packaged and shipped to the jobsite for field installation. Continuous quality control means every part is continually inspected from the time extrusions are received at our facility until delivery. This type of rigorous quality control and inspections ensures the project will be receiving materials that are ready for installation by our highly qualified installation crews.
Field Installation
Through coordinated delivery and installation schedules, materials are brought to the site after mutually agreed sequence schedules and delivery timing is agreed upon. Materials are hoisted to the proper location and set into place using a variety of project appropriate equipment.